Packaging
Panels leave the production plant in packets. The number of panels in a package depends on the type of the panel, its thickness and length. Upon customer’s individual request, panels may be delivered in a non-standard packaging, with different number of panels or different order of panels in a package. However, transport restrictions must be considered, as well as the fact that in certain cases costs of transport might be higher.
Panel transport
Production, packaging, transport and arrangement of panels on a transport mean are subject to Panel Tech planning processes. In case of any individual expectations in this respect, customers should provide appropriate information during order submission in most cases, Panel Tech delivers panels to a site specified by the customer using special open-top vehicles which guarantee transport safety. If the transport is to be arranged by the Customer, a few basic principles should be taken into account:
- panels are loaded at the production plant with use of forklift trucks,
- only technically fit vehicles may be used for the transport of sandwich panels,
- loading platform must be flat and clean, with no sharp protruding parts,
Unloading
Panels delivered to the construction site may be unloaded with use of a forklift truck or a crane. In both cases packets of panels have to be properly secured against damage. Place soft pads with proper width (approx. 15-20 cm) on the fork of the forklift truck or install crane sling securely. While unloading, follow general safety precautions for hoisting equipment operation.
Storage
There are no special requirements for storage of panels before installation if storage period is no longer than one week. It is essential to provide an appropriate number of supports and place them on a flat surface to prevent bending or local damage if the weight of the panels is not distributed evenly on all supports. In case of storing panels for a longer period, packets should be placed on supports with a proper slope, so that rain water is drained naturally. Remember also that there is a risk of vulcanization of foil and metal, as mentioned above. Additionally, panels should be separated with spacers to ensure free airflow.
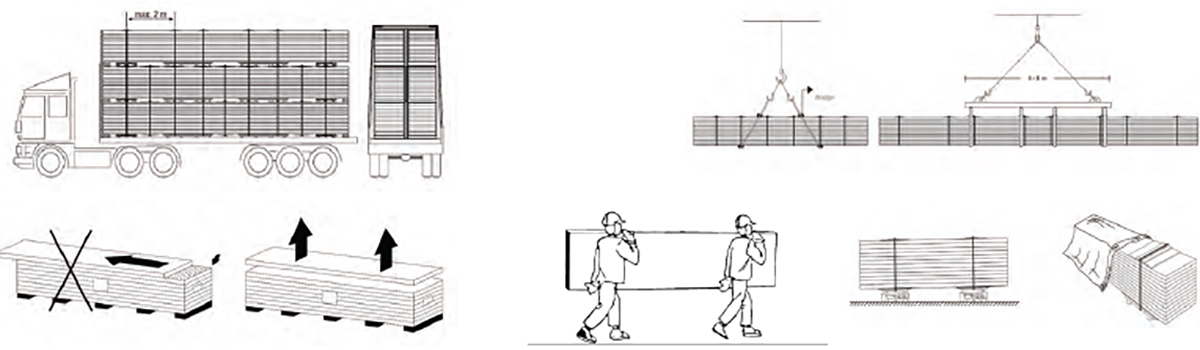
Structure check
Before installation of panels, supporting structure must be checked in terms of its consistency with the design allowable tolerances. Deviation tolerances of purlin, transom and wall deviation from flatness and straightness in lines must be checked with particular care. If any deviations are found, investor’s representatives must be notified. Installing panels on a structure which does not meet the requirements may result in damaging the panels be basis for not being granted the warranty. To avoid any mistakes, panel length and maximum span must be rechecked in accordance with strength tables and permissible panel lengths table.
Basic installation tools:
- driver with adjustable torque
- driver bit for screw over tightening and indenting panel surface,
- cold cutting tool. Angle grinders are not acceptable. Firstly, because of heating of lining edges protective paint and zinc coat is damaged and corrosion centers form. What is more, core may ignite because of contact with sparks and fire, later on it may propagate inside the panel,
- other basic tools, such as meter, level, plate shears, sealant gun,
- suction cup handles would be very useful for transport and installation of panels.,
Installation of Wall panels
PANEL TECH sandwich panels have two sides: external and internal. The internal side is marked with a colored film. Panels must not be installed reversely. An accidental installation reversely may result in a noticeable difference of wall color. Additionally, in relation to the technology of production, external side is always smoother and core adherence to lining is better.
It is recommended that panels are installed in the order in which they are placed in the packet and in the order packets’ delivery. This should reduce the risk of occurrence differences in the color of neighboring panels. Color uniformity should be checked as frequent as possible, particularly in case of metallic colors. To carry out such inspection, after having removed the protective film, watch the surface of the wall at different angles from the distance of approximately 25 meters. If there are any differences, immediately notify the manufacturer.
Panels should be fastened to the structure with use of dedicated galvanized or stainless-steel screws recommended by the manufacturer. Use clutch drivers to install the fasteners. In case of panels with visible fastening system pay special attention to the torque.
When installing a neighboring panel, pay attention to press it properly to the previously installed panel, so the width of the gap between them corresponds to the value specified in the technical drawings. Standard amount and location of fasteners is specified in the reference drawing “location and amount of fasteners” at the end of this section.
Installation of roof panels
When determining the direction of roof panels’ installation, give consideration to the prevailing wind direction. Wind should blow in the direction of the lap joints of the roof panels. Installing panels in the opposite direction may increase the risk of rain water leaking to the interior of the building.
Before installation, check roof rectangularity and position the first panel carefully so it is perpendicular to the eaves. This will eliminate the risk of joint offsets in the neighboring panels and then facilitate further installation of eaves flashing and gutter. Remove protective film from the inner side before installing the next panel. Check linearity of the lower joint before panel installation. Possible local deformations may hinder assembly of the panels and impair the appearance of the underside of the roof.
Panels should be fastened with PANEL TECH recommended screws. The warranty is void if the distances between the edges of the panels and fastener axes, specified in the catalogue drawings, are not followed. Their application significantly reduces the risk of roof leaking and increases mechanical endurance of the fastening.
Fastener must be tightened so that optimal pressure on metal sheet and tightness of an opening is ensured. If the pressure is too low, it can cause inefficient load capacity of fastener and lack of tightness. On the other hand, if the pressure is too high, it can cause deformation of metal sheet around the fastening as well as overstraining of screws.
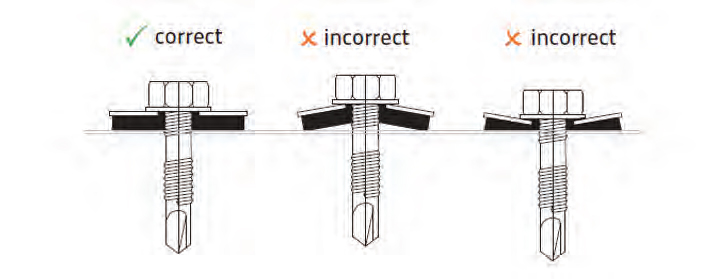
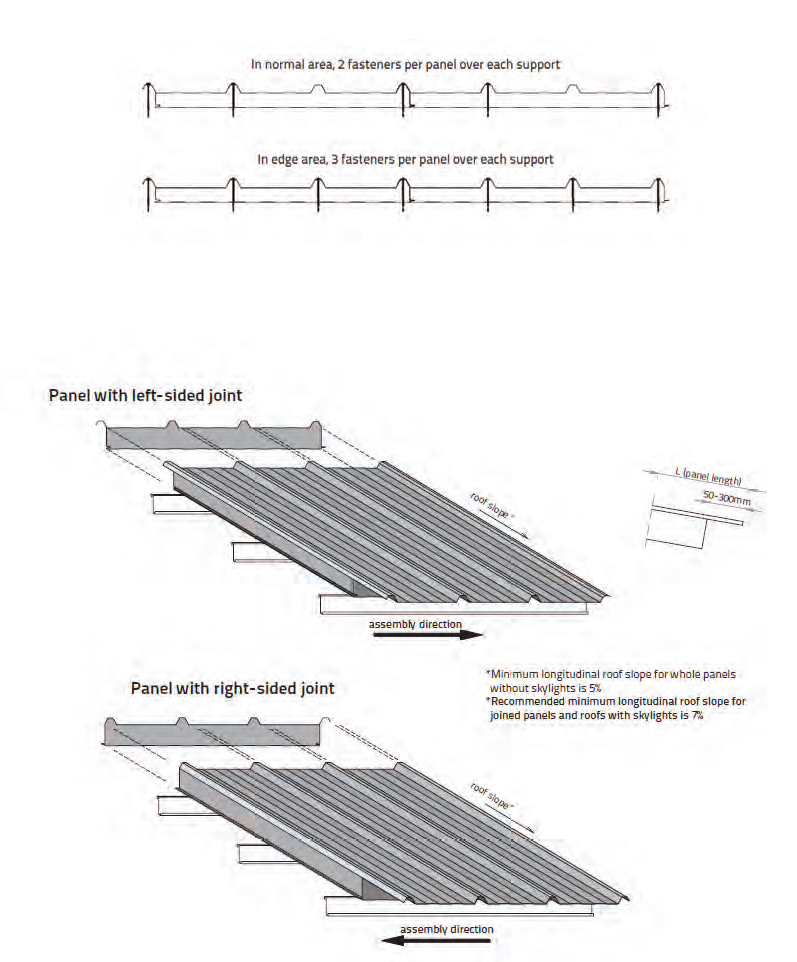